The first three blogposts were intended to give you a broader perspective on the Lockheed Vega project. But I think it’s now time to leave that behind and start to talk business! It’s time to jump into the nitty-gritty of the development. And I chose the topic of “barometer”, because it was one of the first systems implemented in our Vega.

Like in most other aircraft, there are three instruments in the Vega that rely on barometric sensors. Namely the Altimeter, Vertical Speed Indicator (VSI) and the Airspeed Indicator (ASI). Those are barometric instruments, because they use ambient air pressure to “compute” their respective parameters. On the right you see a simplified diagram of the barometric system of the Vega and how the instruments are connected.
Altimeter
The altimeter is nothing more than a barometer. It measures the ambient pressure by means of a diaphragm on the static port and correlates it to the airplane’s altitude based on the standard atmospheric model, with correction for the local atmospheric conditions. And yes, FSX/Prepar3D provides the developer with all the variables to simulate an altimeter, with variables and events for the Kollsman correction. HOWEVER, I’ve always been intrigued by a good malfunction simulation and FSX/P3D doesn’t cut it when it comes to that.
So instead of relying on what FSX/P3D feeds us, the system simulation Lockheed Vega is doing the altitude calculation independently, needing nothing but the ambient pressure from the sim. With this approach, I am able to introduce errors that go way beyond FSX’s “the altimeter isn’t working”. E.g. what happens when the static port is clogged up? How do the response time of the instruments change when switching to the alternate source? How does it feel when you can’t just press ‘B’ to set the altimeter? Find out with our Lockheed Vega!
VSI
For the vertical speed indicator I use a similar approach as described above, but differentiated over time to calculate the ascent/descent rate. Also similar questions arise – the VSI relies on an open static port. If it’s clogged up the instrument will indicate a much slower rate of ascent/descent.
ASI
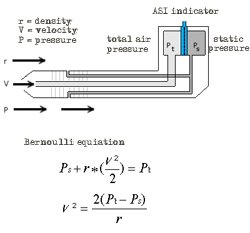
The airspeed indicator of an aircraft is essentially pressure sensor as well. But, different to altimeter and VSI, it takes two source: the static pressure from the static port and the total air pressure from the pitot tube. As the plane moves through the air, the air gets pressed into the hole of the pitot tube and directed into the airspeed indicator in the cockpit where it presses against a diaphragm with the static pressure pushing against it on the other side of the chamber. And because the dynamic pressure is higher the faster you fly, the diaphragm moves further thus indicating a higher speed.
You can clearly work out how this instrument reacts when one of the pressure ports are clogged up (or you simply forgot to remove the cover before the flight). For instance, if the pitot tube is clogged, the dynamic pressure inside your instrument will be the same as the static pressure – your instrument shows “0”, no matter how fast you really fly.
But some other interesting questions arise with the pitot-static principle. The ASI is essentially only accurate when you’re at level flight, because when your aircraft is at an angle, less air is pressed into the pitot tube, thus you’ll get a slower speed indicated and the same error can be observed when you yaw your aircraft left or right off axis.
Development
The pitot-static system and it’s three instruments are already fully integrated into the Lockheed Vega. Provisions are also made to simulate different errors – e.g. the wrong indication when one of the ports are blocked. All the coding for this is done in C++, interfacing the sim through SimConnect and setting custom L:variables to set, for instance, the needle animation.
I hope this article was informative for you and I’ll see you next time when I’ll start talking about electrics.